Ducting Pressure Losses
Fired heater designers utilize ducting for many purposes in a fired heater design. They are used for connecting flue gas plenums to stacks, distributing combustion air to burners, transfering flue gas to and from air preheat systems, etc. The pressure losses through ducting pieces may be individually analyzed or the may be analyzed as a system.
We will first explore ducting losses by looking at the individual pieces. The following formulas and coefficients are from the American Petroleum Institute Practice API RP533.
Straight duct run friction loss:
Dp = (0.002989 * Fr * rg * Vg2)*Le/De
Where,
Dp = Pressure drop, inH2O |
Fr = Moody friction factor |
rg = Average gas density, lb/ft3 |
Vg = Velocity of gas, ft/sec |
Le = Equivalent length of piece, ft |
De = Equivalent diameter of piece, ft |
And for round duct,
De = Diameter
And for rectangular duct,
De = (2 * Width * Height)/(Width + Height)
Moody friction factor, Fr
We can use the Colebrook equation to solve for the friction factor, with the roughness factor selected from the following:
Duct surface | Roughness |
Very rough | 0.01 |
Medium rough | 0.003 |
Smooth | 0.0005 |
90° Round section elbow loss:
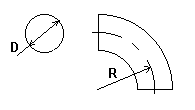 |
Dp = Vh * Cl |
Where, |
Vh = Velocity head of gas, inH2O |
Cl = Loss Coefficient From Table |
Radius/Diameter(R/D) | Coefficient(Cl) |
0.5 | 0.90 |
1.0 | 0.33 |
1.5 | 0.24 |
2.0 | 0.19 |
90° Rectangular section elbow loss:
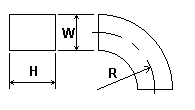 |
Dp = Vh * Cl |
Where, |
Vh = Velocity head of gas, inH2O |
Cl = Loss Coefficient From Table |
Height/Width(H/W) | Radius/Width(R/W) | Coefficient(Cl) |
0.25 |
0.5 |
1.25 |
|
1.0 |
0.37 |
|
1.5 |
0.19 |
0.50 |
0.5 |
1.10 |
|
1.0 |
0.28 |
|
1.5 |
0.13 |
1.00 |
0.5 |
1.00 |
|
1.0 |
0.22 |
|
1.5 |
0.09 |
4.0 |
0.5 |
0.96 |
|
1.0 |
0.19 |
|
1.5 |
0.07 |
Elbow of any degree turn loss:
This may be used for a rectangular or round duct elbow of N ° turn.
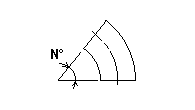 |
Dp = Vh * C90 * N/90 |
Where, |
Vh = Velocity head of gas, inH2O |
C90 = Loss coefficient from above for 90° turn |
N = Number of degrees of turn |
Sudden contraction loss:
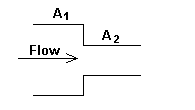 |
Dp = Vh * Cl |
Where, |
Vh = Velocity head of gas, inH2O |
Cl = Loss Coefficient From Table |
Area2/Area1(A2/A1) | Coefficient(Cl) |
< 0.2 | 0.34 |
0.2 | 0.32 |
0.4 | 0.25 |
0.6 | 0.16 |
0.8 | 0.06 |
Gradual contraction loss:
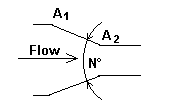 |
Dp = Vh * Cl |
Where, |
Vh = Velocity head of gas, inH2O |
Cl = Loss Coefficient From Table |
Included Angle(N°) | Coefficient(Cl) |
30 | 0.02 |
45 | 0.04 |
60 | 0.07 |
No contraction change of axis loss:
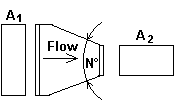 |
Dp = Vh * Cl |
Where, |
Vh = Velocity head of gas, inH2O |
Cl = Loss Coefficient From Table |
Included Angle(N°) | Coefficient(Cl) |
<=14 | 0.15 |
Sudden enlargement loss:
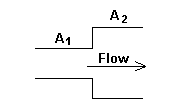 |
Dp = Vh * Cl |
Where, |
Vh = Velocity head of gas, inH2O |
Cl = Loss Coefficient From Table |
Area1/Area2(A1/A2) | Coefficient(Cl) |
0.1 | 0.81 |
0.3 | 0.49 |
0.6 | 0.16 |
0.9 | 0.01 |
Gradual enlargement loss:
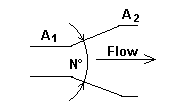 |
Dp = Vh * Cl |
Where, |
Vh = Velocity head of gas, inH2O |
Cl = Loss Coefficient From Table |
Included Angle(N°) | Coefficient(Cl) |
5 | 0.17 |
10 | 0.28 |
20 | 0.45 |
30 | 0.59 |
40 | 0.73 |
Sudden exit loss:
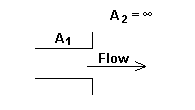 |
Dp = Vh * Cl |
Where, |
Vh = Velocity head of gas, inH2O |
Cl = Loss Coefficient From Table |
Area1/Area2(A1/A2) | Coefficient(Cl) |
0 | 1.0 |
90° Round miter elbow loss:
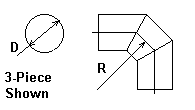 |
Dp = Vh * Cl |
Where, |
Vh = Velocity head of gas, inH2O |
Cl = Loss Coefficient From Curve |
|
90° Rectangular miter elbow loss:
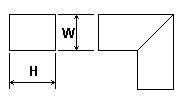 |
Dp = Vh * Cl |
Where, |
Vh = Velocity head of gas, inH2O |
Cl = Loss Coefficient From Table |
Height/Width(H/W) | Coefficient(Cl) |
0.25 | 1.25 |
0.5 | 1.47 |
1.0 | 1.50 |
4.0 | 1.35 |
Pressure loss across stack damper:
This pressure loss is normally accounted for by rule of thumb. This may be 0.5 or 0.25 velocity head. We will use 0.25.
Dp = 0.25 * Vh
Where,
Dp = Pressure drop, inH2O |
Vh = Average velocity head of stack, inH2O |
Draft gain or loss:
The draft gain or loss will be taken based on the height of the upward or downward flow of the flue gas. If the flow is upward, the pressure loss is negative.
Dp = (ra - rg)/5.2 * A
Where,
Dp = Draft gain or loss, inH2O |
rg = Density of flue gas, lb/ft3 |
ra = Density of ambient air, lb/ft3 |
A = Height of gas path, ft |
Velocity head of gas:
Vh = Vg2 * rg / 2 / 32.2 / 144 * 27.67783
Where,
Vg = Velocity of flue gas, ft/sec |
rg = Density of flue gas, lb/ft3 |
Now we can try some of these piece calculations,
Now that we have some procedures for calculating the pressure loss for the various components that we might find in a duct system, how do we use them? The easiest way to analyze a ducting system and keep the pressure points straight, is to organize the system starting from the outlet and proceeding to the inlet. This may seem backwards at first, but when you examine the pressure at a given point in the system, you find that the pressure is always dependent on the downstream pressure. So, it makes sense to always work from outlet to inlet, then you always know the pressure of the outlet of the point you are at. To try this out, we will run the calculations for the simple example shown below.
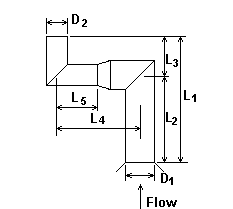 |
For this example, we will assume we are picking up the flow at some point in a system, so we will calculate from the outlet(assumed to be to atmosphere) to the inlet without considering any condition at the inlet. We will assume the process conditions are those in above table. |
So assuming, |
D1 = 4 ft dia. |
D2 = 3 ft dia. |
L1 = 10 ft |
L2 = 7 ft |
L3 = 3 ft |
L4 = 7 ft |
L5 = 3 ft |
Desctription |
DeltaP, inH2O |
Static, inH2O |
Dynamic, inH2O |
Total, inH2O |
Outlet Condition |
0 |
0 |
0 |
0 |
Sudden Exit |
1.1242 |
0 |
1.1242 |
1.1242 |
Straight Duct Run, 2 ft |
0.0136 |
0.0136 |
1.1242 |
1.1378 |
Miter Elbow, 2 Pc |
1.4614 |
1.4750 |
1.1242 |
2.5992 |
Straight Duct Run, 3 ft |
0.0204 |
1.4954 |
1.1242 |
2.6196 |
Gradual Contraction, 45° |
0.0450 |
2.3089 |
0.3557 |
2.6646 |
Miter Elbow, 2 Pc |
0.4624 |
2.7713 |
0.3557 |
3.1270 |
Straight Duct Run, 5 ft |
0.0082 |
2.7795 |
0.3557 |
3.1352 |